WJE PROJECTS
Metallurgical Evaluation of Pipe Welds
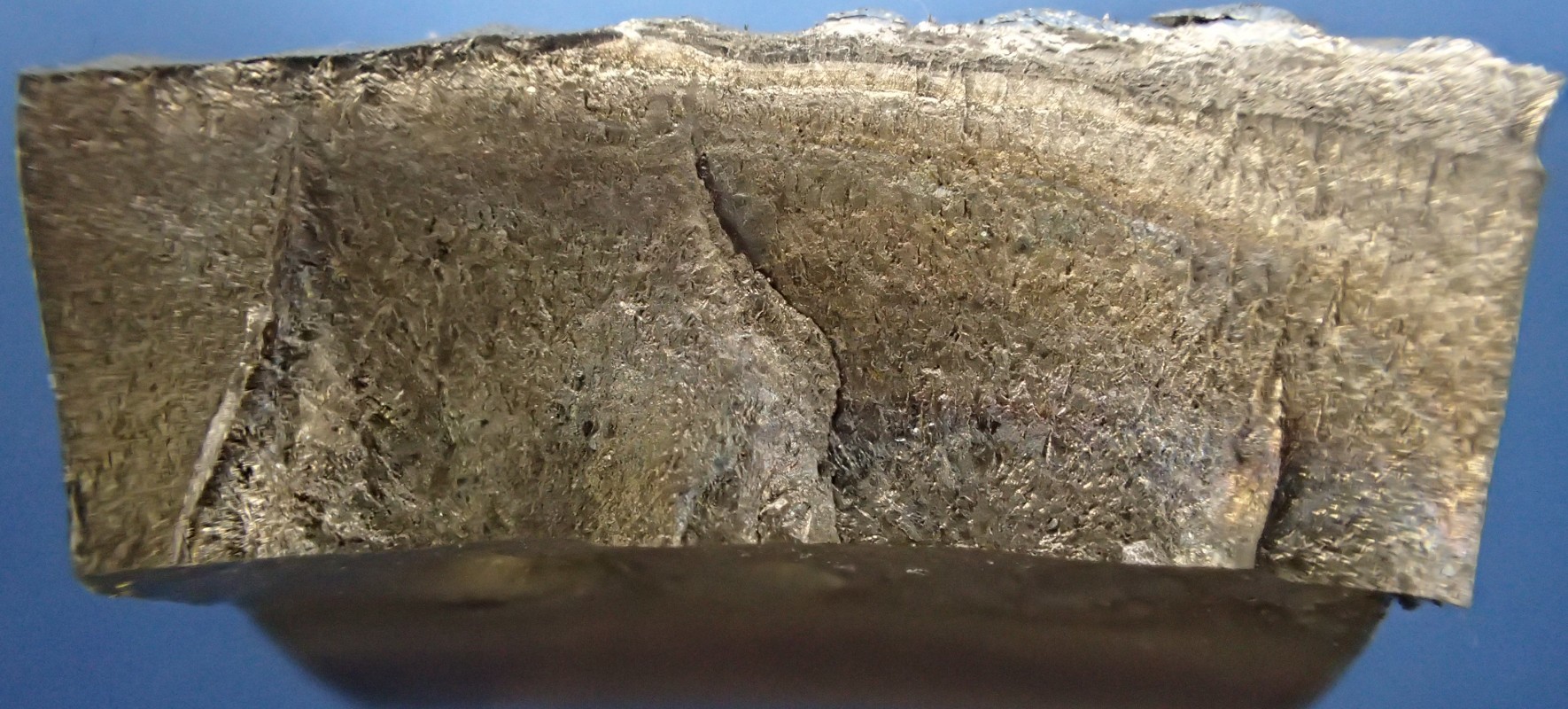
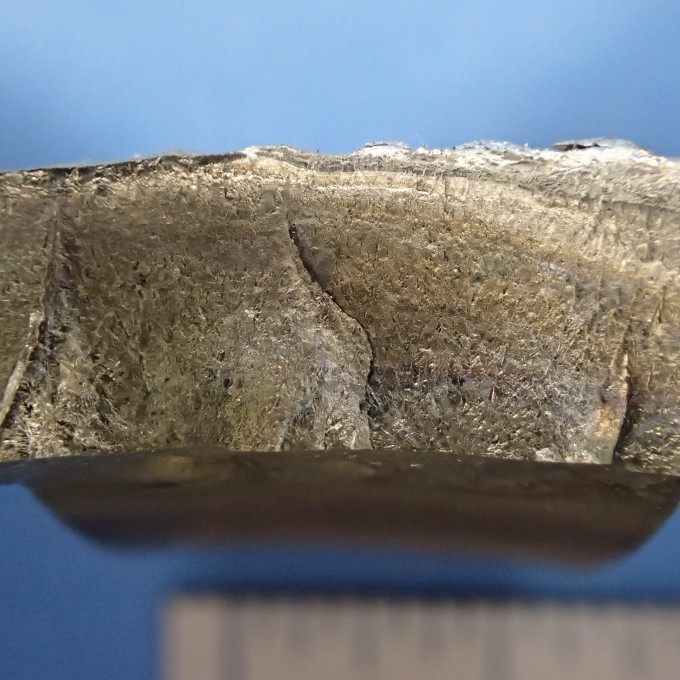
CLIENT |
Industrial Gas Supplier |
LOCATION |
California |
Condensate Service Pipe Weld Cracking Failure Investigation
WJE was engaged to perform a metallurgical evaluation to determine the failure mechanism of the observed cracking in the pipe welds. Three stainless steel pipe components were received that had exhibited leaks. The components included two reducers and a tee-pipe with elbows. All observed leaks were identified as cracking in the circumferential weld region of the pipe components. The original pipe material was 304 stainless steel. The client had made several material changes in an effort to mitigate the leaks, which was assumed to be an environmental cracking problem.
BACKGROUND
A series of leaks occurred at multiple locations along a condensate pipe circuit. The initial response was to make material upgrades based on the assumption that improved material corrosion resistance was required. The subsequent metallurgical investigation determined the leaks were a result of high-cycle mechanical fatigue. The solution was to review the piping circuit design and support system.
SOLUTION
The visual examination identified the cracks for subsequent sectioning to expose the fracture surfaces and create metallographic samples. High-magnification images of the fracture surfaces were obtained using a scanning electron microscope. Chemical analysis of the reducer and flange was conducted using optical emission spectrometry to identify weld and base-metal composition. Select weld fracture samples were longitudinally sectioned, mounted, and polished for metallographic observations. Microhardness testing was performed on the metallographically prepared cross-sections: the base metal, the heat-affected zone, and the weld.
Laboratory observations indicated that the pipes did not exhibit significant corrosion or any indication of an environmental cracking mechanism. The fracture characteristics were consistent with a fatigue fracture mode. The chemical composition and microstructure of the components met the material requirements, with no anomalies detected that could have contributed to the fractures. Small cracks initiated on the inner-diameter surface at the root of the weld; this is typically a result of increased localized stress due to the geometry. WJE recommended a review of the pipe system and supports, including monitoring for vibration in the pipe circuit and review of inspection plans for similar piping circuits.
RELATED INFORMATION
-
Our metallurgical and applied mechanics engineers provide solutions related to design... MORE >Services | Metallurgy and Applied Mechanics
-
WJE's primary goal of performing a metallurgical failure analysis is to determine the root cause... MORE >Services | Metallurgical Failure Analysis
-
We apply the lessons learned from more than 175,000 projects to provide clients with a full... MORE >Services | Condition Evaluation
-
Our materials scientists provide comprehensive consulting services for the evaluation and... MORE >Services | Materials Evaluation and Testing