WJE PROJECTS
Haystack Landing Bridge
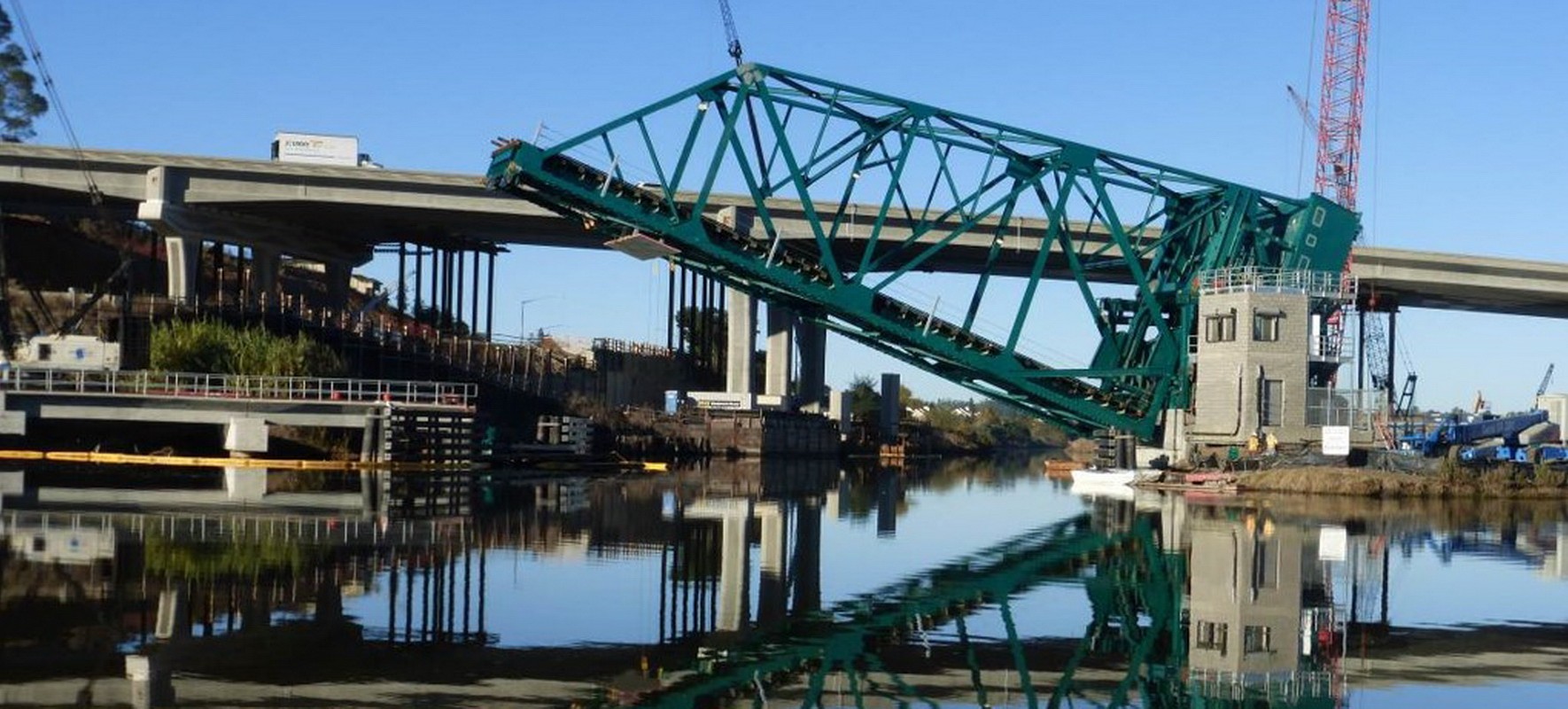
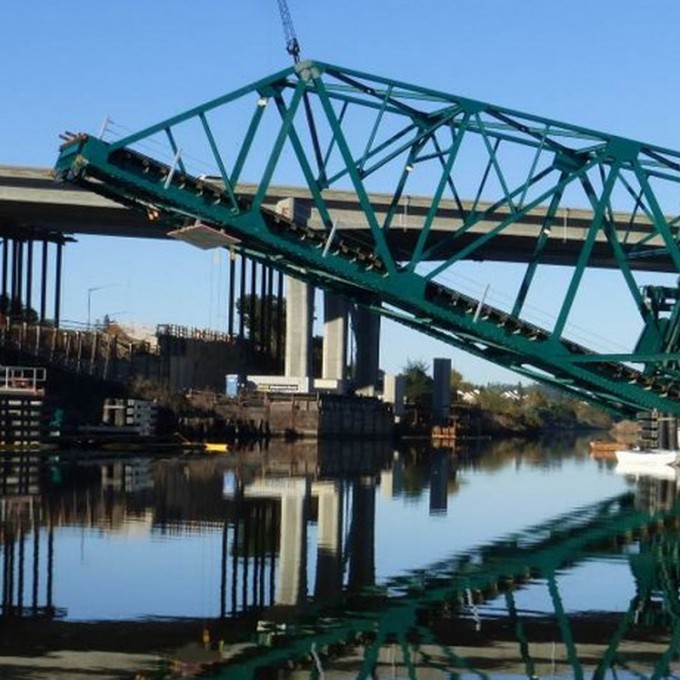
CLIENT |
AECOM |
LOCATION |
Petaluma, CA |
Movable Bridge Relocation and Rehabilitation
WJE was the mechanical and electrical engineer of record for the project and provided design services for the rehabilitation and reconstruction of the movable bascule bridge for the design-build team, which was led by AECOM. WJE also provided comprehensive construction services to ensure satisfactory completion of the work, including on-site assistance throughout construction to assist with the installation, start-up, and commissioning of the bridge.
BACKGROUND
As part of the $428 million project undertaken by SMART to link downtown San Rafael to the Sonoma Airport, Shimmick Construction, Inc. was awarded a $68.7 million contract that included the replacement of the existing Haystack Landing Bridge over the Petaluma River to connect trains between Marin and Sonoma. Rather than refurbish the existing circa 1903 Haystack Landing Bridge at a cost of $20 million, SMART acquired a Scherzer rolling lift bascule railroad bridge from BNSF Railroad in Galveston, Texas, for $4.2 million. The new bridge is expected to have a life span of seventy-five to one hundred years.
SOLUTION
WJE’s design services included a condition assessment of the existing structural and mechanical components as well as design for major mechanical rehabilitation and complete replacement of the electrical power and control systems, including interfacing with the railroad signal system. WJE’s mechanical engineering services included design verification of all existing span drive machinery for conformance to AREMA specifications; fully closed and fully open air buffers and curved and flat tread plates for conformance to applicable specifications; design of new machinery at the high-speed end of the span drive; reinforcement of machinery supports; design of new toe span locks; design of fully open span locks to meet seismic requirements; development of construction staging to maintain uninterrupted rail service; and development of inspection and alignment criteria.
The designed bridge electrical systems consisted of new power and control systems for the movable bridge, including modern PLC logic control and flux vector variable frequency drives. An under-channel installation was developed as part of the design to connect the electric service equipment and associated communications to the bridge operating system. The system design included communications, fire life safety system design, and the integration of all bridge operating systems.
RELATED INFORMATION
-
We are an industry leader in the design, inspection, and repair of heavy movable structures MORE >Services | Heavy Movable Structures
-
Our knowledge of bridge performance is supported by technical expertise in structural... MORE >Services | Bridge Engineering
-
Our independent design review secures a superior level of quality control as well as the... MORE >Services | Design Review