WJE PROJECTS
Fort Madison Toll Bridge
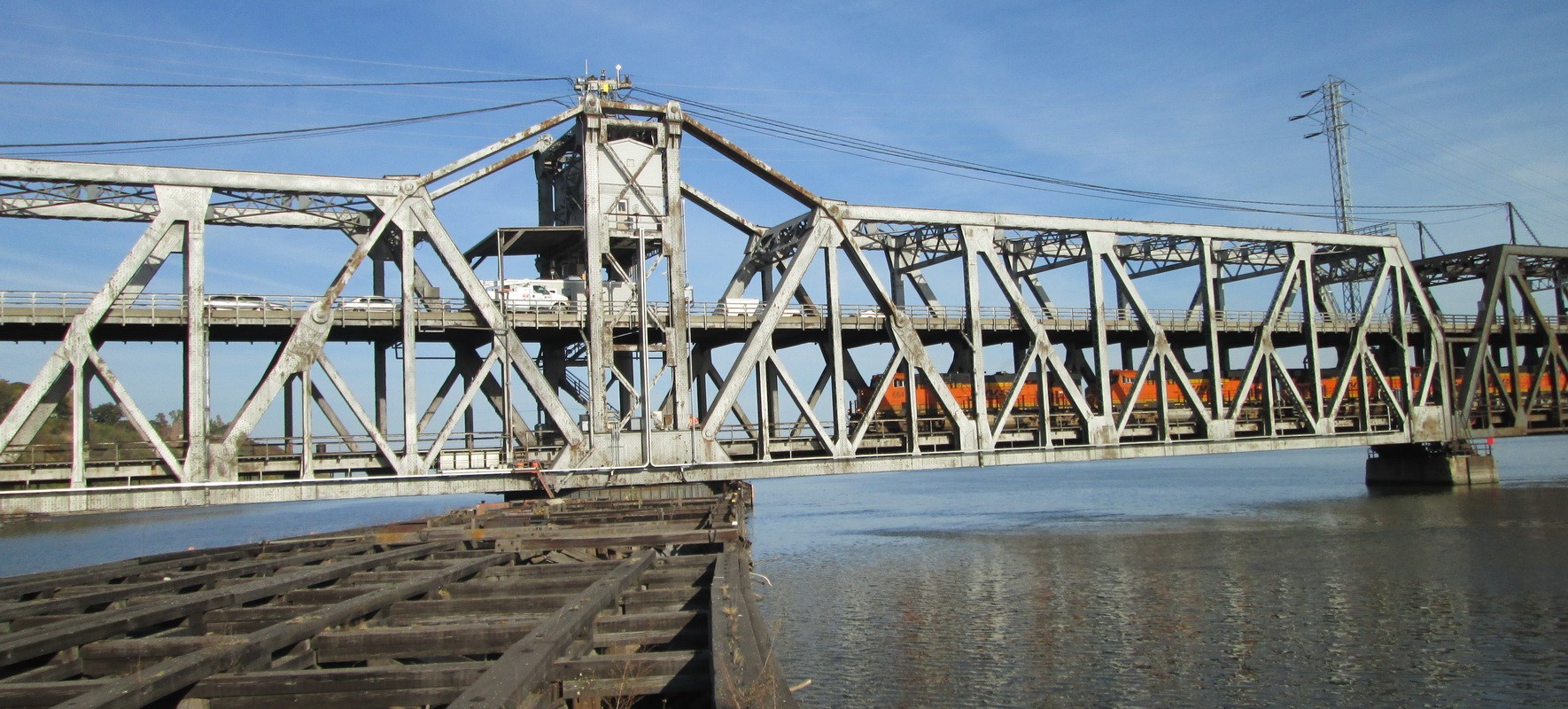
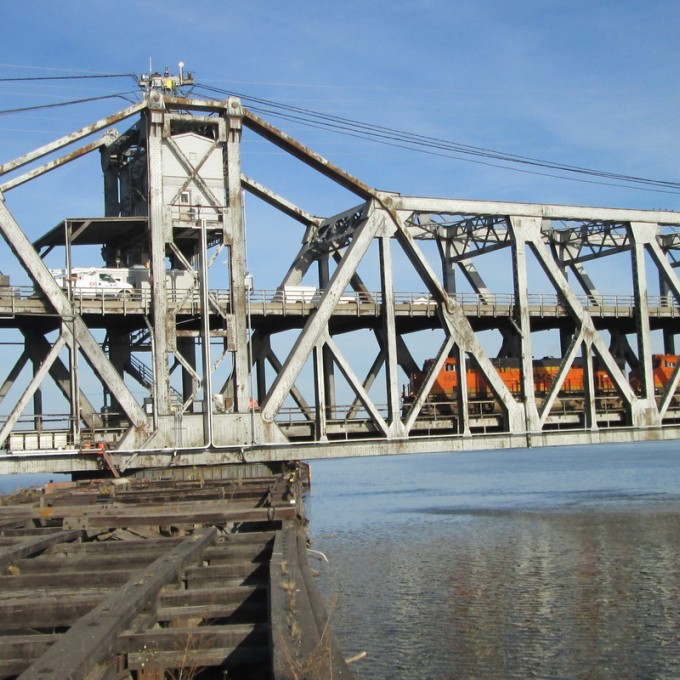
CLIENT |
BNSF Railway |
LOCATION |
Fort Madison, IA |
Electrical and Mechanical Inspection and Design
WJE performed an in-depth inspection and condition assessment of the electrical systems, concluding that the electric power and control installation, as well as both duplicate electric service feeders, were in poor condition and potentially on the verge of failure. Based on these findings, BNSF Railway contracted us to design a replacement power and control system for the bridge. Due to the criticality of the bridge’s operation, BNSF Railway elected to perform the proposed replacement work in stages over a three-year period to maintain operation during replacement.
BACKGROUND
Completed in 1927, Fort Madison Toll Bridge—also known as the Santa Fe Swing Span Bridge—is a double-decker swing-span bridge over the Mississippi River that connects Fort Madison, Iowa, with Niota, Illinois. Privately owned by BNSF Railway, the swinging truss bridge has a two-lane highway on the upper deck and a two-track freight railroad on the lower deck. The bridge machinery and electrical operating systems are located on the moving structure and consist of bridge drive motors and brakes, rail lock motors, and end lift motors. Bridge approaches are provided with vehicular traffic control and navigation lighting. The bridge is provided with a local electric utility service and a fully rated on-site standby generator.
SOLUTION
The initial stage included designing a new aerial and submarine cable system between the bridge’s fixed and moving structures, ensuring that the designed aerial and submarine cable would be unaffected by the rotation of the swing span when transitioning between the fixed and moving structures during bridge operation. The completion of the new electric service feeder system provided the bridge with reliable sources of electric service. The second stage of electric power and control replacement design consisted of the replacement and upgrade of the bridge drive motors, brakes, bridge, and traffic control systems.
The drive system replacements included replacing the motors and drives with modern induction motors and variable frequency drives. Replacing the braking system with electromechanical brakes with modern thruster brakes and drive-initiated dynamic braking enables the operating bridge braking using the new motors and drives and uses the electromechanical brakes as holding brakes. The existing bridge control system consisted of a combination of a programmable logic controller (PLC) and relay logic, but had not been configured as a redundant system. The replacement system, which consists of both the PLC and relay logic, is configured so that the PLC is the primary form of bridge control, with the relay logic acting as backup.
RELATED INFORMATION
-
We are an industry leader in the design, inspection, and repair of heavy movable structures MORE >Services | Heavy Movable Structures
-
Our knowledge of bridge performance is supported by technical expertise in structural... MORE >Services | Bridge Engineering
-
Our professionals contribute their expertise every day to properly designing, constructing, and... MORE >Markets | Infrastructure
-
Our professionals deliver practical repair and rehabilitation services that maximize the... MORE >Services | Repair and Rehabilitation